- What Is Autotransformer? Complete Information Guide
- Three Phase Transformer Diagram
- 3 Phase Transformer Connection Diagram
Using ordinary single-phase transformers in unusual applications can have extraordinary benefits. We'll examine three more configurations here.
Case Eight: Zig-Zag Autotransformer (ZZA). A steel building (under construction) has a temporary 480V, 3-phase, 3-wire feeder for welders and general power. Unfortunately, the contractor encloses the facility without windows, before the busduct feeding the 277V lighting is complete. Non-stock fittings delay energizing the duct. Table 1, (in original article) shows the electrical parameters.
To serve phase-to-neutral loads from an ungrounded 3-phase 3-wire source, use the ZZA connection for a neutral conductor for grounded-wye service. Here, we nippled together three 11/2-kVA transformers connected in this fashion. We added a 480V, 20A enclosed circuit breaker, and connected a 4-conductor No. 6 AWG, Type W flexible cord with a 60A, 480V pin-and-sleeve plug to the breaker line terminals. We wired a 5-conductor No. 10 AWG, Type SO cord between the breaker load side and the lighting-control enclosure. This assembly provided a temporary 480Y/277V, 3-phase, 4-wire branch circuit for fixed low-bay lighting. We bonded the neutral to nearby building steel as required by NEC Sec. 250-5(b). Sec. 450-5(a) recognizes autotransformer use for grounded-neutral derivations. When serving 277V loads, you must solidly ground the ZZA wye point.
3 shows this same isolated transformer connected as a stepdown autotransformer, while Fig. 4 shows it connected as a bucking autotransformer. Variable Transformers Schematics & Wiring Diagrams. Schematics and Wiring Diagrams General Wiring Information Common is used as the third leg in a three phase open delta or as neutral in a three. A three-phase transformer is built for a specific connection and voltage transformation and the unit will have a nameplate with the internal connections shown. When a single unit or bank of three is used, there are four types of connections. The four basic connections are: Y-Y, Y-∆, ∆-Y, and ∆-∆. The first symbol indicates the connection of the primary, and the second symbol is the. See full list on circuitglobe.com. If the application needs a neutral (including 3 phase 4 wire systems), the autotransformer must be ordered with the optional neutral terminals (“3L0U” suffix). This option will provide the customer with a common (H0/X0) neutral connection. Three Phase Transformer Connections The primary and secondary windings of a transformer can be connected in different configuration as shown to meet practically any requirement. In the case of three phase transformerwindings, three forms of connection are possible: “star” (wye), “delta” (mesh) and “interconnected-star”.
Per Sec. 450-5(a)(1), you can't use independent overcurrent protection or disconnecting means between the ZZA set and its connected load. This configuration has phase-to-ground fault currents anywhere on the system divided among the phase connections of this transformer set. Yes, a ground fault of sufficient magnitude and duration downstream of the overcurrent device protecting the autotransformer will cause an outage. However, an equal or greater ground fault upstream will also cause local tripping, and possibly a second simultaneous branch-circuit or feeder overcurrent-device operation somewhere else on the 480V system. You sacrifice some selective coordination with ZZA grounding.
Case Nine: Autotransformer Connection (AT). A maintenance shop needs an industrial-grade 0.60 duty-cycle transformer / rectifier-type arc welder. The facility rents one having single-phase nameplate listed full-load currents of 104A at 200V, 90A at 230V, and 45A at 460V. A supply house delivers the welder strapped for highest-voltage operation: Fitted with a 4-conductor No. 6 AWG, Type SO flexible cord and a 60A, 3-pole, 4-wire pin-and-sleeve plug. For the listed duty cycle, NEC Sec. 630-11(a) permits a multiplier of 0.78 for conductor ampacity in a welder branch circuit. A surplus equipment dealer has coils of 2-conductor No. 8 AWG, Type ACL cable and a suitable transformer in good condition available at minimal cost. The 10kVA four-winding transformer (configured for step up service:parallel 240V windings and series 120V windings) allows the device to handle 20kVA of one phase of a 480V load. This short-term application (using surplus materials) may not be cost-effective in every situation.
The welder is 90 ft from the shop's service switchboard, with the transformer placed at the switchboard. At the welder location, we installed a 60A 600V fused disconnect switch and mating 3-pole, 4-wire pin-and-sleeve receptacle. Table 2 (in original article) shows the electrical parameters.
NEC Sec. 450-4(b) recognizes field-connected autotransformers. Sec. 210-9 mandates the system-neutral connection shown for case nine. Sec. 450-4(a) describes the basic 125% overcurrent-rating requirement for autotransformer applications. We provided a 100A molded-case breaker in the service switchboard for the welder circuit.
Step-up autotransformers (single- and open-delta 3-phase) can serve larger outdoor areas where circuit runs associated with exterior lighting are long, but have only lower-voltage service.
The usual grounding for separately-derived systems is irrelevant to autotransformers, because you have a conductor common to all transformer windings (Sec. 210-9 and 250-23).
Case Ten: Dual Delta/Wye Configuration. At an explosives test facility, an electrical contractor nearly completes installation of a metal clad 12kV tie-breaker switchgear and associated pole line (Table 3, in original article).
The site owns a pair of 3-phase transformers two miles apart; each rated 20 MVA @ 115kV delta-12kV wye. In 1981, the in-house utility operations group energizes one of the transformers (T525) with C-B-A high-side phasing (per the utility). During a 1985 upgrade, they heat up the other (T301) with primary phasing per a government-agency standard, which is A-B-C. Engineering considers this inconsequential during design and construction. (Surely the resident crew could easily fix any phasing problems at the commissioning stage:flopping or rolling 15kV, 750kcmil, MV-90 cables at their terminations would be a simple task!)
The Operations Dept. proposes a working model of the unfinished project to help resolve the problem. A protective-relay electrician assembles six identical 75VA, 480V - 120V machine-tool control-power transformers on a metal panel. Their wiring (identical to that of their larger delta-wye counterparts) gets temporary power from a motor-workbench 480V circuit (Fig. 2, in original article). The electrician uses a magnitude-indicating phase-angle meter on this mock-up while he records and plots voltages and angles. Tables 4a, 4b, & 4c (in original article), show the measurements with out-of-phase primaries, and Table 5 (in original article) shows those with in-phase primaries.
After obtaining a clearance from the serving utility's switchyard, testing for verification of de-energization, and applying personal protective grounds, the line crew reverses phases A and C slack spans on one of the power-transformer primaries. But, before we can place the two transformers in parallel, we need to verify that the respective phase-to-phase 12kV bus voltages are equal at the same instant. (We're dealing with a pair of 3-phase alternating voltages.)
Two linemen securely block open the primary stationary-disconnect shutters in the empty tie-breaker cubicle at the T525 gear. With a racked-out vacuum circuit breaker, we have two sets of 3-phase stabs exposed at their normal medium-voltage potential.
In industrial settings, having an open breaker energized on both sides is unique to a tie circuit.
Six initial phase-to-ground measurements (Table 6, in original article) verify the neutral point is at ground potential for each 12kV bus of the power-transformer pair. It's important to test for the presence of normal 3-phase voltage at the bus and line sides of the racked-out tie breaker. Lastly, we take the crucial three bus-to-line readings (Table 3, in original article). Prior to paralleling, readings must fit the maximum 6 DEGR-delta angle/10%-delta voltage rule of thumb. In this case, bus-to-line voltage for each pair of phase conductors can be no more than 1.2 kV.
The model shows we can't perform in-phase secondary-side paralleling of the two transformers with the existing 115kV bus configuration. The bolted 12kV fault level at tie-breaker closing will exceed 350MVA. ANSI-standard delta-wye transformers served in A-B-C phase sequence have an inherent 30 DEGR lagging phase shift in voltage from primary to secondary. If you find reversed high-side phase sequence, then the secondary voltage leads the primary by 30 DEGR. These two 30 DEGR angles add to produce a most-undesirable 60 DEGR mismatch.
What Is Autotransformer? Complete Information Guide
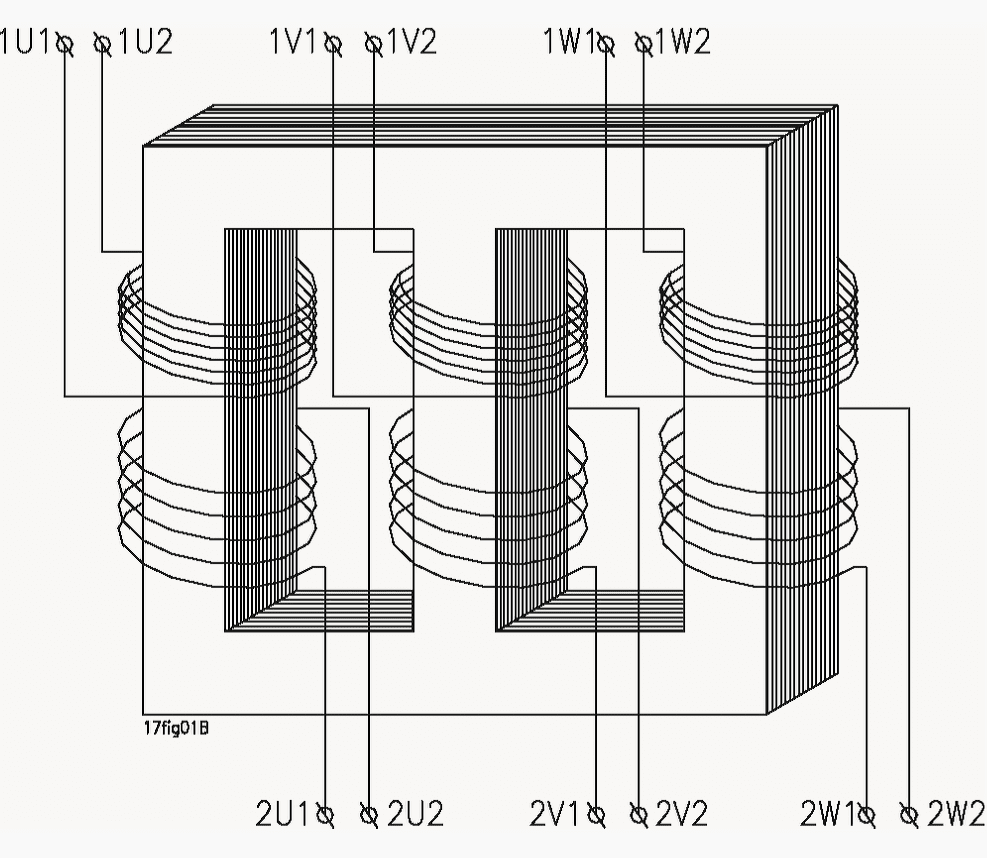
Getting a clearance from the utility to flop incoming 4/0-gauge high-voltage spans between the utility's pole-mounted air switch and our oil breaker (on the T525 high side) is easier than medium-voltage-cable rework.
Article series summary. The 10 configurations in this series are most useful for loads under 15 kVA. With the hookups discussed in this article, you'll find single-phase transformers appropriate where conventional 3-phase single-enclosure transformers may not be suitable for a particular situation or time constraint. Discrete single-phase units in the uncommon arrangements introduced here can be desirable where you need to power a small load, or where lower-capacity, symmetrically connected banks (typically delta-wye, delta-delta, or wye autotransformer) may be too expensive or have unacceptable lead times.
Remember, you must carefully consider these transformer-connection capabilities and limitations, the requisite overcurrent protection, load ratings, and grounding specifics. These connections provide economical alternatives to the more-conventional.
Your ability to apply technical competence to electrical systems is a valuable asset to any commercial or industrial operation. Circuits detailed in this article can give your facility the money- and timesaving advantages of using limited quantities of ordinary, easily obtained single-phase transformers.
Three phase transformer connectionsIn three phase system, the three phases can be connected in either star or delta configuration. In case you are not familiar with those configurations, study the following image which explains star and delta configuration. In any of these configurations, there will be a phase difference of 120° between any two phases.Three phase transformer connections
Windings of a three phase transformer can be connected in various configurations as (i) star-star, (ii) delta-delta, (iii) star-delta, (iv) delta-star, (v) open delta and (vi) Scott connection. These configurations are explained below.

Star-star (Y-Y)
- Star-star connection is generally used for small, high-voltage transformers. Because of star connection, number of required turns/phase is reduced (as phase voltage in star connection is 1/√3 times of line voltage only). Thus, the amount of insulation required is also reduced.
- The ratio of line voltages on the primary side and the secondary side is equal to the transformation ratio of the transformers.
- Line voltages on both sides are in phase with each other.
- This connection can be used only if the connected load is balanced.
Delta-delta (Δ-Δ)
- This connection is generally used for large, low-voltage transformers. Number of required phase/turns is relatively greater than that for star-star connection.
- The ratio of line voltages on the primary and the secondary side is equal to the transformation ratio of the transformers.
- This connection can be used even for unbalanced loading.
- Another advantage of this type of connection is that even if one transformer is disabled, system can continue to operate in open delta connection but with reduced available capacity.

Star-delta OR wye-delta (Y-Δ)
- The primary winding is star star (Y) connected with grounded neutral and the secondary winding is delta connected.
- This connection is mainly used in step down transformer at the substation end of the transmission line.
- The ratio of secondary to primary line voltage is 1/√3 times the transformation ratio.
- There is 30° shift between the primary and secondary line voltages.
Delta-star OR delta-wye (Δ-Y)
- The primary winding is connected in delta and the secondary winding is connected in star with neutral grounded. Thus it can be used to provide 3-phase 4-wire service.
- This type of connection is mainly used in step-up transformer at the beginning of transmission line.
- The ratio of secodary to primary line voltage is √3 times the transformation ratio.
- There is 30° shift between the primary and secondary line voltages.
Three Phase Transformer Diagram
Open delta (V-V) connection
Two transformers are used and primary and secondary connections are made as shown in the figure below.Open delta connection can be used when one of the transformers in Δ-Δ bank is disabled and the service is to be continued until the faulty transformer is repaired or replaced.It can also be used for small three phase loads where installation of full three transformer bank is un-necessary.The total load carrying capacity of open delta connection is 57.7% than that would be for delta-delta connection.Scott (T-T) connection
Two transformers are used in this type of connection. One of the transformers has centre taps on both primary and secondary windings (which is called as main transformer). The other transormer is called as teaser transformer.Scott connection can also be used for three phase to two phase conversion.The connection is made as shown in the figure below.3 Phase Transformer Connection Diagram
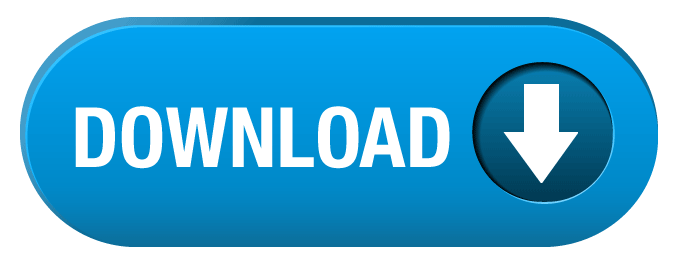